Laser & Folding
Laser Cutting & Engraving
Here at Stable Fabrication, where we offer a comprehensive package encompassing design, manufacturing, and delivery. Equipped with cutting-edge CAD/CAM software and led by expert precision engineers, our in-house team excels at crafting detailed product design drawings using modern techniques.
Metal Folding
Metal Bending & Forming
At Stable Fabrication we offer various types of forming. From our 2.5mm 60 ton brake press to hydraulic press, hand folder and fly presses.
We can shape products using male and female tooling designed in house to your requirements and can also roll and hand manifulate complex parts.
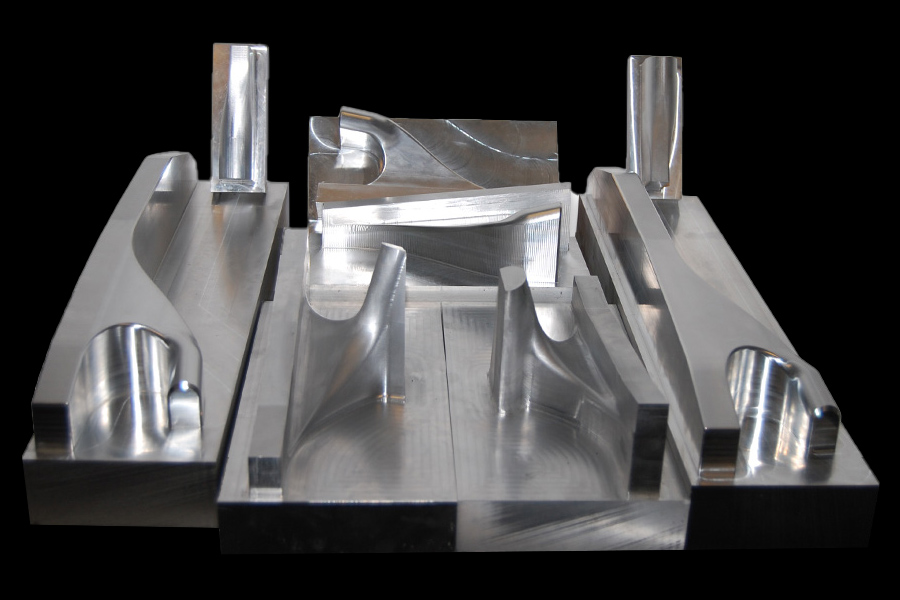